For detailed information, other images and documents, please select individual articles from the following table.
Register now and access more than 150,000 products






Variants
Register now and access more than 150,000 products
High-strength bonding
- Very high adhesive strength
- Viscoplastic adhesive with low foaming behaviour
Proven adhesive properties
- Tested adhesion for "stay-in-place formwork elements" by MPA Braunschweig
- Tested stress group D4 in accordance with DIN EN 204 by ift Rosenheim
- Tested heat resistance in accordance with DIN EN 14257 (WATT 91) by ift Rosenheim
Versatile applications and adheres to a wide variety of materials
- Very good adhesion to a wide range of substrates, such as marble, synthetic stone etc.
- Can subsequently be powder-coated (+200°C/30 minutes)
- Can be sanded and painted over
- Quick reaction time with high functional strength after just 15 minutes
- Fast and uniform hardening up to 4 mm joints
- High resistance (short-term against diluted acids, alkalis and solvents)
- Resistant to weathering and ageing
- Silicone- and solvent-free
- Tested adhesion for stay-in-place formwork elements by MPA Braunschweig
- Tested stress group D4 in accordance with DIN EN 204 by ift Rosenheim
- Tested heat resistance in accordance with DIN EN 14257 (WATT 91) by ift Rosenheim
- French VOC emissions class A+
*Lost formwork elements: The wood cement flat-pressed panels are used in building construction for ring beam formwork, ceiling edge formwork and lintel formwork. The formwork is encapsulated in concrete and remains in the element, which is why they are called "lost formwork".
- Permanent formwork elements = The wood cement flat-pressed panels (24 mm thick floor panel and 10 mm thick wall panel) are used in building construction for ring beam formwork, ceiling edge formwork and lintel formwork. The formwork is encapsulated with concrete (ceilings with a thickness of 160 mm, thicker ceilings of 180 and 200 mm must be evaluated on a case-by-case basis) and remains in the element, therefore also called "permanent formwork".
- The test report 5131/2446a with expert opinion by letter from the Materials Testing Institute Braunschweig confirms that permanent formwork with wood cement flat-pressed panels (L=10/24) bonded with multi-purpose power adhesive is suitable for ceilings up to a thickness of 160 mm. Ceilings with a thickness of 180 and 200 mm must be evaluated on a case-by-case basis.
- The viscosity of 1C-PUR adhesives when processed at +15 °C is approximately double that when processed at +25 °C.
- Sunlight discolours the adhesive but does not affect the adhesive strength.
- Bonding aluminium, copper, brass: Only on chemically pre-treated or coated surfaces: these materials cannot be permanently bonded in an age-resistant manner without appropriate pre-treatment of the bonding surfaces.
- Powder-coated workpieces and all metals must always be cleaned with Aluminium cleaner type 60 (art. no. 0892 130 030 / 0892 130 031).
- Powder coatings with PTFE components cannot be reliably bonded without pre-treatment (e.g. plasma process).
- Pressing pressure: for surface bonding ≥0.015 N/mm²
- for solid wood/solid wood bonding ≥1 N/mm²
- For glue joint thicknesses ≥2.5 mm, the setting, pressing and curing times are significantly longer, glue joint thicknesses ≥5 mm are not possible.
- If moisture is expected to have an impact, the glue joints/bonding surfaces must also be sealed/protected with a suitable sealing compound!
- When gluing metal with absorbent materials (e.g. wood, construction materials etc.), moisture can gradually penetrate the glue joint through the absorbent material and reach the metal surface where it can cause corrosion damage to the metal. The metallic bonding surface must therefore have suitable corrosion protection, such as paint, powder-coating etc.!
- When bonding different materials (with different expansion properties), the glue joint dimensions must be adapted according to the long-term behaviour.
- The bonded workpieces should not be painted until after the adhesive is fully cured. If they are painted too early, blisters could form in the paint.
- As aluminium surfaces and properties are difficult to define, we always recommend that you obtain sufficient information from the supplier to enable you to choose the appropriate pre-treatments for your particular bonding application. Sufficient preliminary tests are necessary.
- In the production and processing of stainless steel, auxiliary materials such as wax, oils, etc. are often used which cannot be simply wiped clean. It has been shown that after cleaning with solvents, grinding or (even better), sandblasting the surface, followed by repeated cleaning with solvents delivers considerably better bonding results.
- Zinc-plated sheets should always be protected from permanent moisture. To prevent the formation of "white rust", any moisture that occurs must be prevented from coming into contact with the bonding surface!
- Bonding larch: 1K-PUR adhesives must never be used for bonding larch surfaces in outdoor areas. The substance "arabinogalactan" which is contained in the wood, or forms within it, considerably weakens the bonding strength! No problems have been identified with PVAC and EPOXI adhesives.
- When bonding solid wood, the adhesive should preferably be applied to both bonding surfaces.
- The adhesive is mildly foaming and is therefore well-suited to use on slightly uneven surfaces. The pressing time must be adjusted according to the thickness of the glue joint.
- For bonding solid wood in outdoor applications, suitable tests should be performed to determine the optimum permanent bond depending on the type of wood, weather intensity, surface protection and geometry of the glue joint.
- Skin-forming and joining times, as well as the respective pressing and processing times required, are influenced by criteria such as material, temperature, amount applied and air moisture, amongst others. As a result, they can only be precisely determined through independent tests. The installer should add appropriate safety margins for the specified reference values.
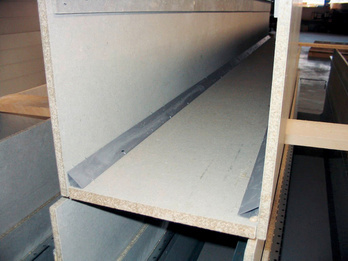
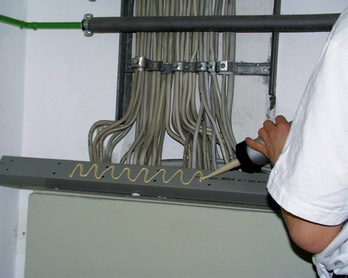
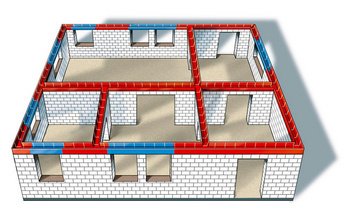
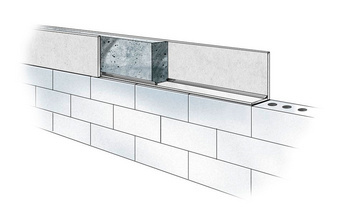
MONTAGELIM | |||||
Multi-klæbemasse med stor trækstyrke 0893 100 110 | Multifiberklæbemiddel 0893 100 115 | PUR Rapid 0892 100 102 | Montagelim, uden opløsningsmiddel 0893 100 100 | ||
PVC (ikke blød PVC!) | ⎷6 | ⎷6 | - | ⎷2 | |
Silicones | - | - | - | - | |
Styrofoam | ⎷ | ⎷ | ⎷ | ⎷ | |
Painted surfaces | Painted surfaces (2K paints, baking enamels, KTL, coil-coated sheets) | ⎷5 | ⎷5 | ⎷5 | - |
Wood & wood-based materials | Wood (auch MDF, Chipboard) | ⎷ | ⎷ | ⎷ | ⎷ |
HPL-laminar ore paneler (Restopal, Ultrapas) | ⎷ | ⎷ | ⎷ | ⎷ | |
Decorative paneler | ⎷5 | x | x | ⎷ | |
Cork | ⎷ | ⎷ | ⎷ | ⎷ | |
Stone & building materials | Concrete | ⎷3 | ⎷3 | ⎷3 | ⎷3 |
Bituminous backgrounds | - | - | - | - | |
Gas concrete, plaster, plasterboard | ⎷3 | ⎷3 | ⎷3 | ⎷3 | |
Artificial stone (Korian, Varicor) | ⎷ | ⎷ | ⎷ | ⎷3 | |
sensitive natural stone (e.g marmor) | ⎷ | ⎷ | ⎷ | - | |
Stone | ⎷ | ⎷ | ⎷ | ⎷ | |
Cement-based fibreboards | ⎷3 | - | - | ⎷3 | |
Others | Emalje | ⎷5 | ⎷5 | ⎷5 | - |
Glas | - | - | - | - | |
Glass fibre | ⎷ | ⎷ | ⎷ | - | |
Mirror | - | - | - | - | |
Porcelain, ceramics, tiles | ⎷ | ⎷ | ⎷ | - | |
Papir | ⎷ | ⎷ | ⎷ | ⎷ | |
Pap | ⎷ | ⎷ | ⎷ | ⎷ | |
Fabric | - | - | - | - | |
Læder | ⎷ | ⎷ | ⎷ | - | |
Metals | Aluminium | ⎷4,1 | ⎷4,1 | ⎷4,1 | ⎷1 |
Lead | - | - | - | - | |
Stainless steel | ⎷5 | ⎷5 | ⎷5 | ⎷1 | |
Copper | ⎷5,4,1 | ⎷5,4,1 | ⎷5,4,1 | ⎷ | |
Brass | ⎷5,4,1 | ⎷5,4,1 | ⎷5,4,1 | x | |
steel/iron | ⎷5,4,1 | ⎷5,4,1 | ⎷5,4,1 | ⎷1 | |
Zinc | - | ⎷ | ⎷ | ⎷ | |
Plastics | ABS | ⎷4,2 | ⎷4,2 | ⎷4,2 | ⎷2 |
GRP | ⎷5 | ⎷5 | ⎷5 | ⎷2 | |
Rubber/neopren | ⎷5 | ⎷5 | ⎷5 | - | |
Hard foams | ⎷ | ⎷ | ⎷ | ⎷2 | |
PE | - | - | - | - | |
PMMA | - | - | - | ⎷2 | |
Polyamide | ⎷ | - | - | - | |
Polycarbonate | ⎷5 | - | - | ⎷2 | |
Polystyren (ikke skum!) | - | - | - | - | |
PP | - | - | - | - | |
PTFE | - | - | - | - | |
1. Prime with Primer for Metal primer (art. no. 0890 100 66) 2. Prime with Primer for P/W/S (art. no. 0890 100 62) 3. Pre-treat with Deep-Penetrating Primer (art. no. 0890 545 10) 4. Pre-treat with Activating Cleaner (art. no. 0890 100 60) 5. Pre-treat with Cleaner Type 60 (art. no. 0892 130 030, 0892 130 031) 6. Pre-treat with Cleaner Type 10 (art. no. 0892 100 10) *Surface must not be moistened with lotus effect |
Optimisation table | ||
Surface/material | Optimisation steps* | Notes |
Polyamide | Varioprimer safe + easy | – |
Wood, plywood, MDF, wood products and cork | Dedusting | – |
HPL laminated panels (Resopal, Ultrapas) | Cleaner type 60 | – |
Enamel, porcelain, ceramic, tiles | 1. Cleaner type 60 2. Varioprimer safe + easy | – |
Concrete, mineral mortar, plaster and cement fibre board | 1. Remove dust 2. Deep-penetrating primer | – |
Artificial stone (Corian, Varicor) | Cleaner type 60 | – |
Anodised aluminium | 1. Activating Cleaner 2. AdhesionPlus metal primer | – |
Aluminium (AlMg3, AlMgSi1) | 1. Basic cleaning with cleaner type 60 2. Sand lightly with a very fine abrasive fleece 3. Post-cleaning with cleaner type 60 4. Activating Cleaner 5. AdhesionPlus metal primer | – |
Non-ferrous base metals (brass, copper, bronze etc.) | The use of AdhesionPlus metal is mandatory! | |
Stainless steel (rustproof) | – | |
Steel (St 235 etc.) | In components susceptible to corrosion: 2C PU or epoxy corrosion protection required! | |
Zinc-plated steel (hot-dip or zinc plated) | Corrosion formation | |
Zinc | Formation of white rust when moisture is present | |
Powder coatings | Cleaner type 60 | Preliminary testing is recommended for applications involving significant forces or a damp environment. |
(PES, EP/PES) | ||
2C top-coat, water or solvent based (PUR, acrylic) | Varioprimer safe + easy | Due to the large number of paints available, this information is only a guide. Where necessary, perform preliminary tests. |
2C primers, water or solvent-based | Varioprimer safe + easy | – |
(PUR, acrylic, epoxy resin) | ||
Cathodic dip coating | Activating Cleaner | – |
(E-coating) | ||
Coil-coat coating | Activating Cleaner | – |
ABS | 1. Activating Cleaner 2. AdhesionPlus primer for P/W/S | – |
GFRP (unsaturated polyester), gelcoat side or SMC | 1. Basic cleaning with cleaner type 60 2. Sand with “very fine” or grain 60-80 fleece and then vacuum 3. Post-cleaning with cleaner type 60 | Adhesive surface must be protected against UV radiation (opaque cover). |
Hard PVC | Cleaner type 10 or type 60 | – |
* Follow the corresponding sequence of the individual steps |
Multi high-strength adhesive is used for gluing house door panels, stairway steps, handrails, baseboards, strips, for fixing supports for false floors, stay-in-place formwork elements made of wood-cement flat-pressed panels, for processing natural stone, for window and door construction, window sills, laminate claddings, carports, pergolas, sign fixing, as well as for general repairs and assembly.
The application surfaces must be clean, dry and free of grease. For pre-treatment, please refer to the optimisation table in the technical data sheet.
Adhesive is applied on one side to one of the bonded parts as a bead, or applied over the whole surface using a toothed spatula. The bonded parts must be joined within the skin formation time and pressed until functional strength is achieved.
For more information, please refer to the technical data sheet.
Select RAL-colour code
!! NOTE: On-screen visualisation of the colour differs from real colour shade!!